石油煉制是現代工業(yè)的基礎,提供了90%以上的交通運輸燃料和化工原料,是世界上最大、最重要的加工工業(yè)之一。而煉油工業(yè)除常減壓、焦化等少數幾個過程外,80%以上的過程為催化反應過程,催化劑成為實現原油高效轉化和清潔利用最經濟、最靈活、最有潛力的關鍵核心技術,是煉油技術進步最活躍的領域。
中國石油年煉油能力已接近2億噸,催化劑年使用量約7萬噸。但在“十二五”之前,中國石油除了在催化裂化催化劑和硫黃回收催化劑領域具有傳統(tǒng)優(yōu)勢外,其他重要的煉油催化劑研發(fā)還處在起步階段,高水平煉油系列催化劑的開發(fā)成為制約公司煉油技術進步、加快實施國際化戰(zhàn)略的瓶頸。
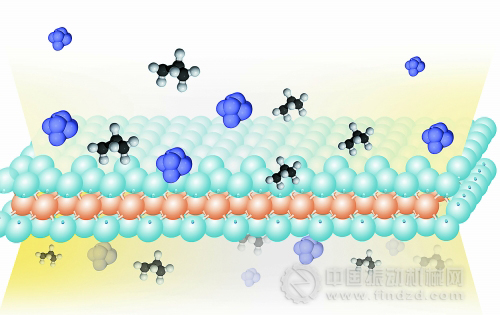
煉油催化劑作用機理示意圖
快速突破催化劑核心技術,開發(fā)具有自主知識產權的煉油系列催化劑,消除瓶頸、補齊短板,建立完整的煉油技術鏈條,盡快形成中國石油煉油業(yè)務的新優(yōu)勢,全面提升中國石油的煉油技術水平,成為擺在廣大科技工作者面前迫在眉睫的一項重要任務。
歷史是何其相似,新中國成立之初,煉油工業(yè)處于一窮二白的起步階段。為打破國外技術封鎖,老一輩科技工作者在石油部的統(tǒng)一組織下,開展了自主研發(fā)催化劑的大會戰(zhàn)。煉油催化劑成為我國煉油工業(yè)的基石,其中生產高級航空汽油的硅鋁小球催化劑為我國國防建設做出了重大貢獻,被稱為名副其實的“爭氣劑”。
如今,煉油工業(yè)面臨原油重質劣質化、過程環(huán)保綠色化、產品清潔高質化等嚴峻挑戰(zhàn)。針對這一緊迫需求,科技管理部會同煉油與化工分公司通過頂層設計,組織大團隊、集中大投入,全面布局重要煉油系列催化劑的研發(fā),堅持自主創(chuàng)新、重點跨越、支撐發(fā)展、引領未來,承擔行業(yè)技術創(chuàng)新責任的目標,于2010年適時啟動實施“煉油催化劑研制開發(fā)與工業(yè)應用”重大科技專項。專項由石油化工研究院牽頭,蘭州石化、撫順石化、西南油氣田和中國石油大學等26家單位近700名科技人員進行為期4年的協(xié)同創(chuàng)新,重點攻關。
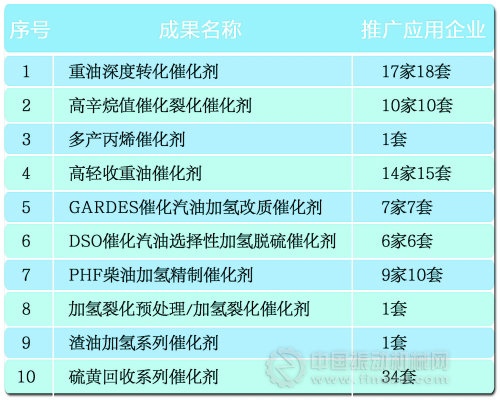
中國石油自主研發(fā)主要煉油催化劑工業(yè)應用情況
“十二五”期間,通過重大科技專項的實施,以催化裂化催化劑成功拓展海外市場、汽柴油加氫系列催化劑全面支撐油品質量升級等為代表,自主創(chuàng)新的技術從無到有,從少到多,中國石油在煉油催化劑關鍵領域取得了重大突破,同時帶動催化新材料、催化反應過程和催化劑生產技術的全面提升,取得了豐碩成果。廣大科技人員團結拼搏、攻堅克難,向集團公司黨組交出了一份圓滿的答卷:攻克了56項關鍵技術,研制開發(fā)了六大類、21個系列52個品種的催化劑新產品和8個品種的催化新材料,開發(fā)出5個工藝包,申請專利154件,認定技術秘密67項,催化劑累計生產銷售超過9萬噸,在54家企業(yè)的111套工業(yè)裝置上實現應用,新增效益20億元以上,整體技術達到國際先進,先后榮獲國家科技進步獎二等獎2項,集團公司一等獎4項。
催化裂化催化劑研發(fā)繼續(xù)保持優(yōu)勢,開發(fā)出重油深度轉化、提高汽油辛烷值、多產丙烯等四大系列17個牌號的新型催化劑,在國內外50余套裝置工業(yè)應用,并成功進軍海外高端市場。硫黃回收系列催化劑在國內外34套工業(yè)裝置得到應用,為裝置達標排放和節(jié)能減排做出新貢獻。汽柴油加氫催化劑在20余套汽柴油加氫裝置成功應用,成為中國石油汽柴油質量升級的主體技術。

催化劑與煉油分子“親密接觸”
加氫裂化和固定床渣油加氫催化劑研發(fā)取得突破,成功實現工業(yè)應用,填補了中國石油在該領域的空白。開發(fā)的高性能NaY分子篩、低成本合成β分子篩等催化新材料成為高性能催化劑開發(fā)的基礎。催化裂化及加氫催化劑生產成套技術攻關取得成功,集成開發(fā)出5萬噸/年催化裂化催化劑、5000噸/年渣油加氫催化劑和1000噸/年非負載加氫催化劑生產技術工藝包,為公司煉油催化劑業(yè)務發(fā)展和生產基地建設提供了技術支持。
通過持續(xù)攻關,提高了石油化工研究院煉油催化劑創(chuàng)新基地和蘭州、撫順兩個催化劑生產基地的研發(fā)生產水平,催化、重質油加工、清潔燃料生產三個重點實驗室和催化裂化催化劑與工藝、加氫催化劑與工藝兩個中試基地的研發(fā)能力和裝備水平實現了質的飛躍,自主創(chuàng)新能力得到大幅度提高。專項攻關培養(yǎng)和凝聚了一支技術精、作風硬、服務優(yōu)、勇于奉獻的創(chuàng)新團隊,他們已經成長為中國石油煉油技術進步的排頭兵和主力軍,是公司發(fā)展的寶貴財富。
進入“十三五”,面臨低油價成為新常態(tài)的挑戰(zhàn),煉油催化劑的研發(fā)在滿足更高標準油品質量升級、煉油產品結構調整、提升重油加工水平、做大做強做優(yōu)公司催化劑產業(yè)需求方面,將重點開展基于“分子煉油”理念的催化劑結構設計、納米化功能化新材料開發(fā)、高效低耗催化劑清潔生產技術等研究工作,使煉油催化劑開發(fā)實現技術模型化、平臺化、成套化,滿足集團公司煉化技術發(fā)展需求,推動中國石油煉油催化劑業(yè)務總體水平比肩國際一流,具備全面參與國際競爭的實力。
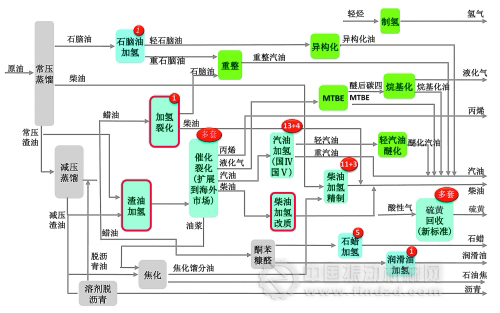
中國石油通過煉油催化劑重大專項新增3個過程(藍底紅框)的催化劑,原有4個過程(藍底)的催化劑水平大幅提升,自主研發(fā)占全部催化過程的63%。
亮點技術
1 汽柴油加氫系列催化劑
石油化工研究院和中國石油大學聯(lián)合開發(fā)了催化汽油預加氫催化劑、選擇性加氫脫硫催化劑等9個牌號汽油加氫系列催化劑,形成了DSO和GARDES汽油加氫成套技術,實現了汽油深度脫硫、降烯烴和保持辛烷值,已在公司的13套裝置應用,占同類裝置的54.4%,支撐了中國石油汽油質量升級。PHF和FDS系列柴油加氫精制催化劑在10家煉廠13套裝置成功應用,為公司柴油質量升級提供重要支撐。“滿足國家第四階段汽車排放標準的清潔汽油生產成套技術開發(fā)與應用”榮獲2015年國家科技進步二等獎。
2 渣油加氫催化劑
重大專項項目組成功開發(fā)了孔結構靈活調控、活性金屬非均勻分布等6項關鍵技術,攻克了適合渣油大分子擴散的特種大孔道載體制備難關,設計并研制出分別具有梯度孔、雙峰孔、通暢孔、集中孔特色的4大類12個牌號固定床渣油加氫催化劑;實現了多種催化劑功能的優(yōu)化級配,最大化發(fā)揮了催化劑脫硫、脫殘?zhí)康裙π?,已在大連西太平洋石化公司渣油加氫裝置上成功完成工業(yè)應用試驗,保障了裝置的長周期、安全、平穩(wěn)運行,總體達到國際先進水平,填補了中國石油在渣油加氫催化劑領域的空白。
3 硫黃回收催化劑
硫黃回收是將硫化氫等有毒氣體轉化為單質硫,實現變廢為寶保護環(huán)境,是煉油、化工和天然氣凈化過程的重要環(huán)節(jié)。
西南油氣田公司研發(fā)出了4種類型9個牌號的系列硫黃回收催化劑,開發(fā)形成了常規(guī)及低溫克勞斯、有機硫水解、硫化氫選擇性氧化、克勞斯尾氣加氫水解等技術,整體水平國內領先,優(yōu)勢領域達到國際領先水平,已在重慶天然氣凈化總廠、獨山子石化公司、廣西石化公司等企業(yè)的34套裝置實現應用,國內市場占有率達到75%。
4 加氫裂化催化劑
加氫裂化技術是唯一能在重油輕質化的同時直接生產車用清潔燃料和優(yōu)質化工原料的工藝技術。
石化院開發(fā)出了活性穩(wěn)定性好、中間餾分油選擇性高、異構性能強的PHC-03加氫裂化催化劑,在大慶石化120萬噸/年加氫裂化裝置成功實現工業(yè)應用,液體產品收率達到99.37%,與柴油和航空噴氣燃料收率相比提高3%,柴油凝點低5攝氏度,尾油BMCI值低2個單位。該催化劑的成功開發(fā)及應用填補了中國石油自主加氫裂化技術領域空白。
5催化裂化催化劑
石化院在國際上提出了正碳離子“晶內產生、晶外傳遞、表面裂解”的重油催化機理新觀點,成為高水平催化劑設計的理論基礎;以自主研發(fā)的Y型分子篩結構二次修飾技術、ZSM-5活性恢復、重金屬涂層捕集等關鍵技術為核心,顯著提高了催化劑抗金屬能力,開發(fā)出了重油高效轉化、提高汽油辛烷值、多產丙烯等系列催化劑,在國內外50余套裝置得到廣泛應用,并成功進入北美高端市場,產生經濟效益12億元以上,使中國石油自主技術生產的產品比例提高到92%,國際競爭力進一步增強。
6 催化新材料
為進一步提高NaY沸石工業(yè)生產技術中產品結晶度和硅鋁比,中國石油依靠自主研發(fā)的多項專利和專有技術,針對高硅NaY分子篩性質特點,通過營造“晶核形成”和“晶體生長”兩種不同化學環(huán)境的技術方法,開發(fā)出具有晶化時間短、結晶度高和較高硅鋁比的高性能NaY沸石合成成套技術,滿足了生產高性能催化材料的生產急需,以此為原料生產的分子篩活性組分在LDO-75、LDO-70等19種工業(yè)催化劑中獲得大面積成功應用。此類材料的成功開發(fā)為今后研發(fā)系列新型催化劑奠定了材料基礎。